From Accidental Discovery to Circular Mission
What started as a chance finding in a chemistry lab in Amsterdam has grown into a promising scale-up with international ambitions. Plantics, based at Cleantech Park Arnhem, develops innovative, biobased, circular materials based on a unique resin and natural fibers. Their sustainable applications can now be seen in products such as building materials, traffic signs, plant pots, and chairs.
The origin of Plantics lies at the University of Amsterdam, where Professor Gadi Rothenberg and Albert Alberts were experimenting with biofuel production. “The experiments failed,” says Kwinten Snijders Blok, Head of Operations at Plantics. “But a sticky substance appeared — a resin — with very special properties.” This accidental discovery turned out to be the foundation for an entirely new thermoset, biobased material.
Bio-Resin
A thermoset is a polymer material that, once hardened, keeps its shape and does not soften when heated (unlike thermoplastics, like a plastic bag, which can be melted and reshaped). What makes the Plantics resin unique is that, unlike conventional thermosets, it can be reused as a binder: “This means we can make a chair from hemp fibers and Plantics resin. Both the fibers and the resin can later be fully reused, without needing to shred the chair,” explains Kwinten.
The resin is made from ingredients derived from agricultural residues such as sugar and vegetable oil production. This closes the loop: from raw material to product and back again. The material is also suitable for outdoor use — rare for biobased products — and biodegrades naturally if it ends up in the soil. This prevents the creation of microplastics if products accidentally enter nature.
An ‘accidental discovery’ became the basis for a completely new thermoset, biobased material.
An 'accidental discovery' became the basis for a completely new thermoset, biobased material.
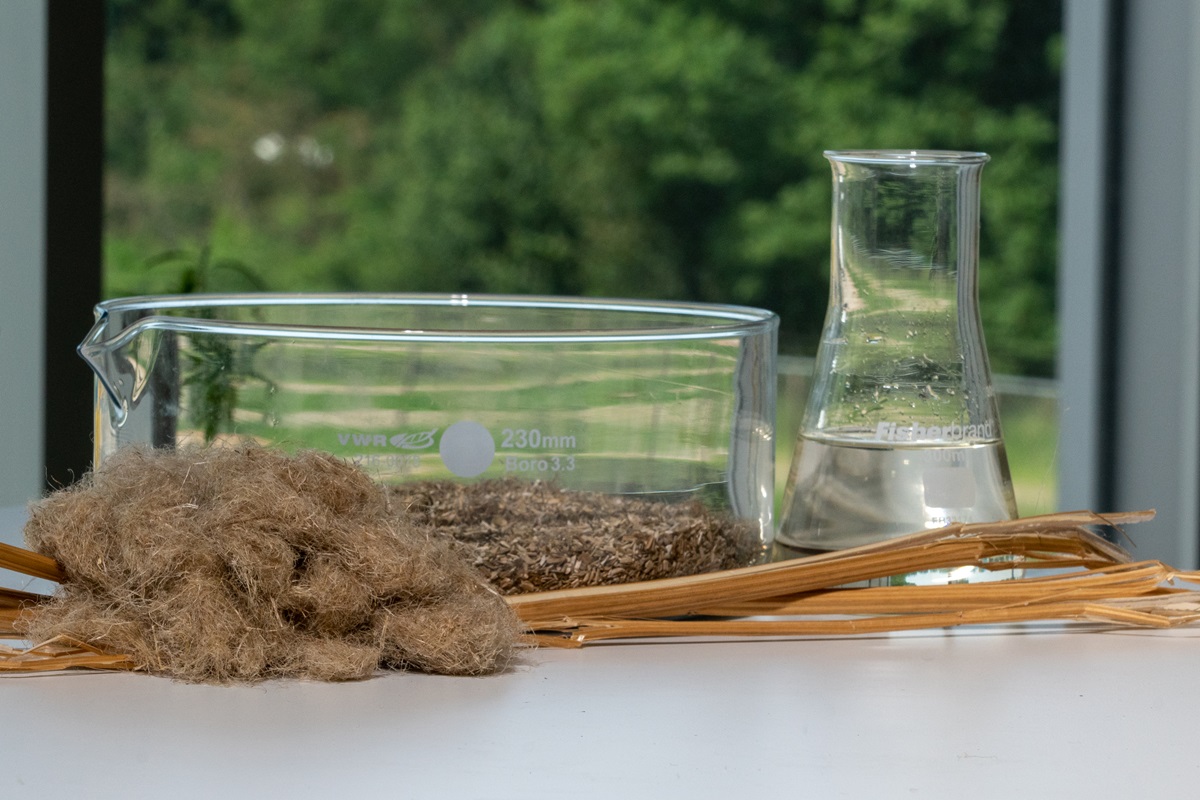
Hemp Composite
In 2017, Plantics became a startup led by Wridzer Bakker. The company grew rapidly, partly thanks to collaboration with the Drenthe furniture manufacturer Vepa. “They were looking for a sustainable alternative to their foam cushion filling,” says Kwinten. Plantics had also developed a composite with hemp fibers and proposed this solution. “Hemp is ideal,” he explains. “It grows incredibly fast, absorbs a lot of CO₂, and leaves the soil healthier.”
Producing the hemp composite is not simple. “Natural materials are not always predictable,” Kwinten notes. “But the result is a material that is strong, durable, and locally produced.” The fibers are grown locally, including in Oude Pekela and Hoogezand (Groningen), often as a cover crop that improves soil structure.
Biobased Traffic Signs
Outside the furniture industry, Plantics is also making an impact. Biobased traffic signs made by Plantics can now be found in Arnhem and Amsterdam. These replace traditional aluminum signs. “Aluminum is often seen as sustainable because it is recyclable,” says Kwinten. “But its production is intensive, polluting, and leaves a heavy ecological footprint.”
Plantics’ ‘green’ traffic signs offer a sustainable alternative: made from hemp fiber and bio-resin, they withstand weather conditions and are biodegradable if they end up in nature. “If a truck hits one, no microplastics break off—only a biological composite that bacteria can break down. Plus, the signs are designed so that components can be easily separated and reused,” explains Kwinten.
Plant Pots
The coated plant pots from Plantics, sold at retailers like Lidl and IKEA, are also fully biodegradable—including the coating. The pots are made from recycled paper and reinforced with a biobased coating based on Plantics resin. “Without our coating, these pulp pots would fall apart after just a few watering sessions,” Kwinten explains. Thanks to the protective layer, they stay sturdy during plant growth and transport but fully biodegrade once placed in soil. “After about 90 days, the pot disappears and even contributes to soil quality,” he says. Thus, the pot serves not only as packaging but as a temporary, nourishing buffer for the plant—a practical and environmentally friendly alternative to the billions of plastic pots used and discarded annually in horticulture.
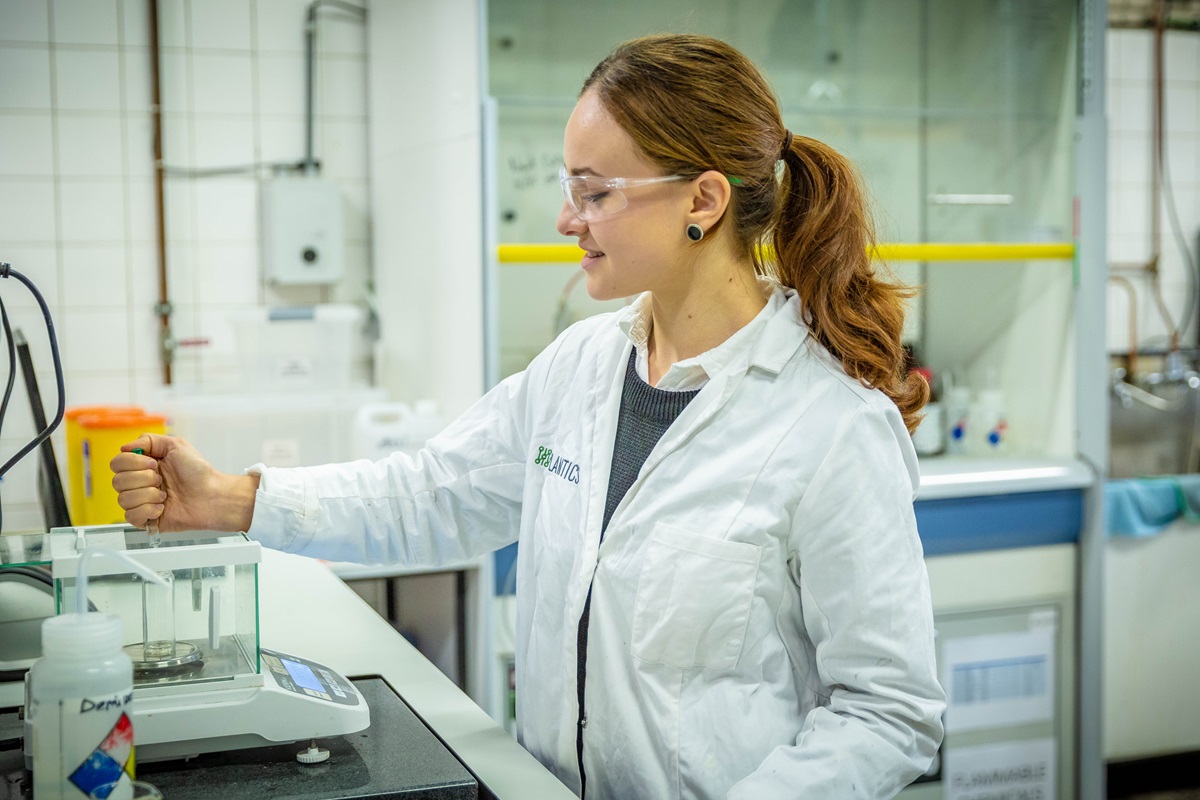
Ecological Footprint
Sustainability at Plantics is not only about the final product but also about how the products are made and used. To make that impact measurable and transparent, the company works with so-called LCAs — Life Cycle Analyses. Such an analysis tracks the entire lifespan of a product: from the origin of raw materials, through production and use, to waste processing or reuse. “We map out how much energy and raw materials a product requires, how much CO₂ it emits, and what happens at the end of its life,” explains Kwinten. This data is not chosen randomly: the analysis follows standardized European guidelines and uses recognized databases.
This information will soon be accessible to consumers via a QR code on each product. “This way, we make visible where our materials come from, what their ecological footprint is, and how they fit within a circular economy,” says Kwinten. “Our mission is to store as much CO₂ as possible in our materials and reuse them endlessly.”
Circular Economy
Collaboration with other companies is important to Plantics. “We believe in strong partnerships. Not only externally with Vepa but also with several other tenants at Cleantech Park,” Kwinten says. The Arnhem cleantech campus provides fertile ground for this: “There’s a green, innovative atmosphere where knowledge sharing happens naturally.”
Besides product development, Plantics is actively involved in education and awareness about sustainability. “We don’t just want to offer people a sustainable product but also explain what it truly means to be circular,” says Kwinten. The company regularly gives presentations and participates in conferences. “Because ultimately, impact starts with understanding: when people know where materials come from, how they are processed, and what happens after use, they can make more conscious choices. Only then can a circular economy really take off.”
Green Ambitions
Plantics currently employs 40 people and works with 15 partners. What started as a discovery in a university lab has grown into one of the most promising biomaterial scaleups worldwide. The leading German Nova Institute selected Plantics’ material as ‘Renewable Material of the Year’ in a global competition.
For example, much particleboard, MDF, and plywood are glued with toxic formaldehyde resins—substances harmful not only during production but also releasing carcinogenic fumes years after use. “Formaldehyde poses a serious health risk, especially indoors,” Kwinten emphasizes. “Our 100% biobased resin offers an environmentally friendly and safe alternative with the same function but without toxic emissions. This contributes not only to a cleaner production process but also to a healthier living environment for the end user.”
“Our ambition? To make a real impact in the global construction and furniture industries,
At Cleantech Park Arnhem, innovations for a cleaner future come to life. This is the perfect place for startups, established companies, government bodies, and educational institutions collaborating on clean technologies for the energy transition and circular economy. Join our active community of forward-thinking businesses today.